Products
- Circular Connectors & Cable Assemblies
- D-Sub Connectors
- IP67 D-Sub Connectors
- D-Sub Backshells
- Micro-D Connectors & Cable Assemblies
- Power-D & Combo Mixed Connectors
- Push Pull Connectors
- D-Sub & Micro D Hardware
- Modular RJ45 Connectors
- USB Connectors
- D-Sub Adapters & Gender Changers
- SCSI .085"/.050"
- .050 Ribbon
- Headers & Receptacles
- Bayonet Connectors
How end-user behavior affects connector selection
There is a lot of conversation around operating temperature, outdoor conditions, and potential ingress when discussing connector ruggedization. But one vital yet overlooked consideration is how the end-user will interact with the connector.
How technicians or staffers use connectors when out in the field or on the factory floor can significantly influence your choice of connector. Those used in situations like test benches, handheld devices, or industrial robotics require a higher level of ruggedization than you might expect. Let’s see how three different end-user behaviors can affect your connector selection.
High-touch applications
Say you’re selecting a connector for equipment that operates in a relatively clean environment. You might opt for a standard model. But it’s just as essential to evaluate how team members will interact with connectors as it is to assess the operating environment.
Dirt, dust, and skin oils from excessive handling are leading causes of connector damage such as bent contact pins, breached seals and corrosive rust—so make sure your connector is properly ruggedized for its intended use.
Rough handling
Yes, we assume field technicians and other team members will handle equipment with care. But it is also important to prepare for the worst—you don’t want one mistake to impact the performance of your entire system.
For connectors that are frequently transported across facilities or are at a high risk of impact, you may want to consider more ruggedized materials.
Popular ruggedized connector materials
- Stainless Steel
- Beryllium Copper
- Nickel-Plated Brass
- Aluminum
Stainless steel is one example of a Rugged Environment Certified material highly rated to protect connectors against likely crushing and dragging related to rough use. Combined with metal sheathing along the cable, you can build out a custom solution impervious to aggressive use conditions.
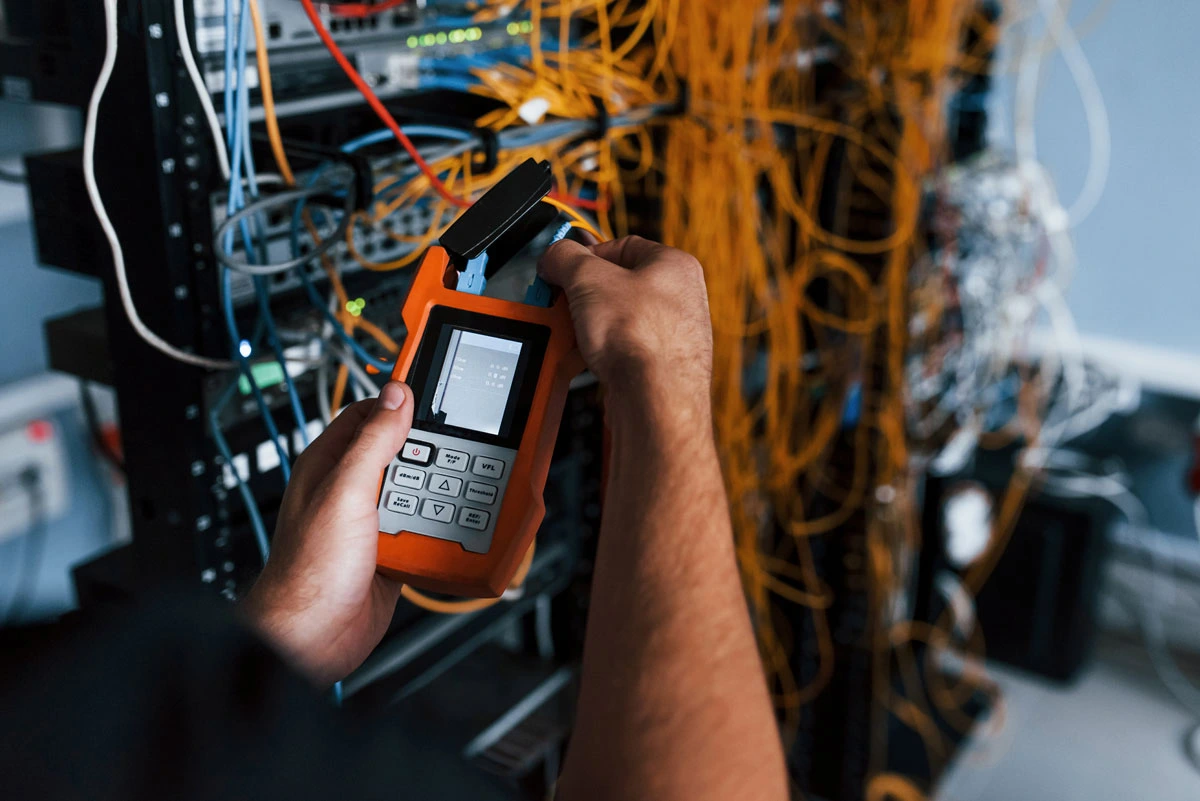
Frequent connect and disconnect
Some connectors are plugged in once and more or less remain so for their lifetime. Other connectors are frequently mated and unmated by technicians, requiring a higher level of durability than a “set-it-and-forget-it” application.
Common situations requiring connectors with high mating cycles
- Test benches that evaluate 5G device performance using a Vector Network Analyzer
- Medical equipment plugged into a variety of different human-machine interfaces
- Industrial robotics, such as an assembly arm with interchangeable tool heads
To combat the excessive wear and tear, explore connectors rated for higher mating cycles. Factors like how contacts are produced, all the way down to their plating method, can affect their lifecycle when used in high-handling applications. Push pull designs with metal or plastic shells feature rapid latch-and-release mechanisms, significantly minimizing the stress incurred by each disconnect.
Mating cycle ratings for three different connector designs
50 Micro Inch Plating |
500 |
QUIK-LOQ push-pull mechanism (plastic shell) |
2,000+ |
QUIK-LOQ push-pull mechanism (metal shell) |
5,000+ |
When exploring connector options, keep in mind how users will interact with equipment. If possible, observe a “day in the life” out in the field, or interview the end-users, who will interact with the connector daily, to learn how it is realistically used.
If you’re only evaluating environmental factors, you might miss out on the complete picture.
If you have any questions about a specific application, please feel free to contact us today.
Go Back