Products
- Circular Connectors & Cable Assemblies
- D-Sub Connectors
- IP67 D-Sub Connectors
- D-Sub Backshells
- Micro-D Connectors & Cable Assemblies
- Power-D & Combo Mixed Connectors
- Push Pull Connectors
- D-Sub & Micro D Hardware
- Modular RJ45 Connectors
- USB Connectors
- D-Sub Adapters & Gender Changers
- SCSI .085"/.050"
- .050 Ribbon
- Headers & Receptacles
- Bayonet Connectors
Design Considerations for Industrial Robotics
Robot design is an exciting and demanding area of engineering, experiencing rapid innovation and development in hardware, software, firmware, mechanical systems, and power systems. Robots are high-computer systems that perform many electromechanical functions, and they require rugged components that can withstand the demands of an industrial environment.
Many of the most influential robot design considerations begin with processing power and electromechanical subsystems. However, there’s much more to robot design than selecting these core components.
Passive components like connectors and cable assemblies are critical for ensuring industrial robotics design reliability. Before you start specifying components for your next industrial robot, take a look at some of these important design considerations that will help ensure uptime and longevity.
Industrial Robot Design Considerations
Industrial robots consist of multiple systems that work together to produce the optimal functionality and performance on the production line. Some of the major systems include:
- A control panel with main system controller module
- Sensor and vision arrays for interacting with the environment
- Electromechanical drive arrays with end effector and manipulator
- A power regulation and management system
- Rugged connector and cable assemblies
- Networking and communications equipment
Each of these subsystems is formalized in ISO-8373 and other standards. All of these elements are present in some form on industrial robots, either in highly integrated electronic modules or connected together from separate systems.
If built on a small number of boards, these designs create EMC challenges due to their high power delivery requirements to electromechanical systems, as well as the presence of many high speed digital components. If separated into different modules, connectors and cable assemblies should be carefully considered and chosen to ensure power delivery and high-speed data transmission between subsystems.
Tasks to Be Performed
One of the most fundamental robot design considerations is the specific fabrication and/or assembly task to be performed. This determines both the components to be selected–particularly the end effector/manipulator–and also the type of robot to be designed.
Other important points like payload, range of motion, and type of motion (translation and rotation) will determine which components are most effective. This may also affect how components can be placed and mounted in the system, underscoring the complexity of some robotics systems. Industrial robots must be placed such that they can handle the electrical/mechanical demands without impeding motion to avoid challenges for data and power connections.
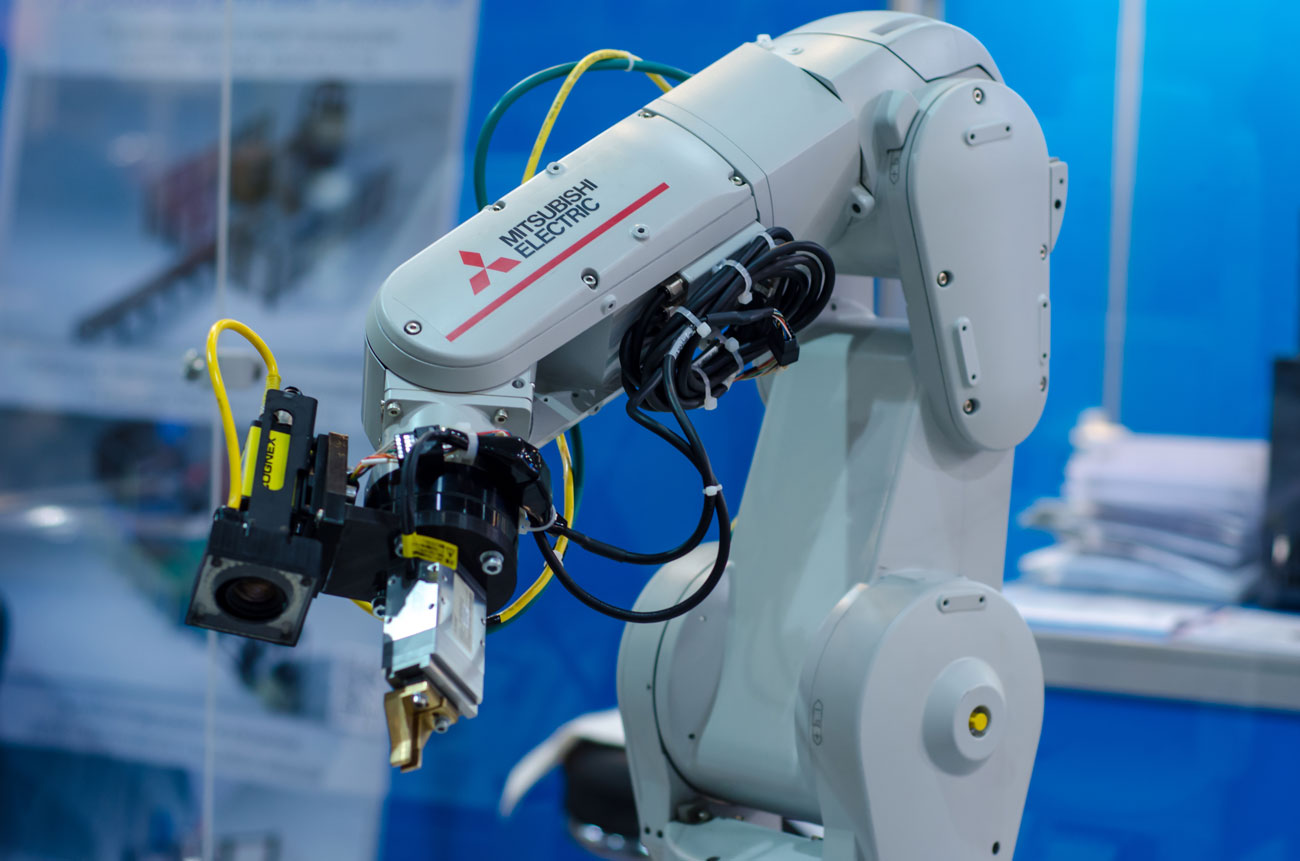
Operating Environment
Robotics designs must also take into account the operating environment. In an industrial environment, a robotic fabrication or assembly system could encounter any of the following situations during operation:
- Power surges or ESD events
- Extreme temperatures that could damage components
- Exposure to corrosive or toxic substances
- Mechanical vibration or mechanical shock
System housing and mounting components are more resilient against these environmental factors compared to electronic assemblies. The circuit board assemblies used in industrial robotics have to meet the highest reliability standards to ensure maximum uptime, with standards meeting or exceeding IPC Class 3. For cable assemblies and connectors, ruggedized connectors are available that are built specifically to withstand these environmental challenges. From a mechanical perspective, examples include over molded and locking connectors that can withstand mechanical vibration or shocks.
As the most common contaminants in an industrial environment are moisture or dust, rugged electrical connectors should be sealed to meet IP67/IP68 requirements. Connectors and housings for assemblies should both be designed to withstand these contaminants as this helps protect circuit boards and other components from ingress. Connector materials and finishes are also important to consider as exposed conductors should not corrode in the deployment environment.
Sensors and Communications Protocols
Sensors and networking protocols are the means modern industrial robots use to interact with other equipment, operators, and the broader world. All modern robots use a suite of sensors, with some located internal to the system and others used as probes to capture measurements. Sensors carry the same reliability considerations as rugged connectors, meaning they must be chosen to withstand the operating environment and any extreme operational conditions listed above.
Communication and networking in an industrial environment typically occurs over a wireless protocol, or over CANBus, Ethernet, or a serial connection via RS-232/422/485. Industrial robotics systems require rugged connector housings for this application to carry data over these wired interfaces with maximum reliability.
Ruggedized versions of standard connector assemblies are available and provide many benefits in these environments, along with cabling that can withstand the same environmental challenges. The same considerations apply to high speed/high frequency connections, although these interfaces need to provide low-loss connections to controlled-impedance cables for reliable data transfer.
Power Delivery
Finally, industrial robotics require power delivery, both at the system’s main power management stage and to subsystems so that fabrication/assembly tasks can be performed. Power system form factors are being driven ever smaller, which creates noise and heat challenges in modern industrial robotics.
Thermal challenges are often surmounted by taking advantage of heat sinking and some advanced materials to aid heat dissipation. Radiated and conducted EMI around a system has to be solved at the board level, as well as at the cable assembly and connector level through use of shielding and a clear grounding strategy.
The Importance of Cables and Rugged Connectors
Each subsystem in industrial robotics products carry their own unique design considerations. Connectors and cable assemblies play an important role in ensuring these robotics systems provide reliable power distribution and data between these subsystems across their lifespan.
For robotics systems with precise form factor limitations, manufacturers of rugged connectors can customize a solution for industrial-grade applications. For designers that want maximum reliability, the above considerations in robotics design will help ensure high reliability and uptime.
When you need rugged connectors for robot design and engineering that can withstand deployment in harsh environments, look to NorComp for standardized or customizable interconnect solutions. NorComp’s product lines are Rugged Environment Certified (REC) and are ideal for use in robotics, military, industrial equipment, and other demanding applications. Contact NorComp today to learn more about our standard or custom interconnect solutions.
Go Back