Products
- Circular Connectors & Cable Assemblies
- D-Sub Connectors
- IP67 D-Sub Connectors
- D-Sub Backshells
- Micro-D Connectors & Cable Assemblies
- Power-D & Combo Mixed Connectors
- Push Pull Connectors
- D-Sub & Micro D Hardware
- Modular RJ45 Connectors
- USB Connectors
- D-Sub Adapters & Gender Changers
- SCSI .085"/.050"
- .050 Ribbon
- Headers & Receptacles
- Bayonet Connectors
Medical devices | Making the right connection
Selection Issues for Medical Connectors
How are connectors and terminals different in medical device design?
To understand the many requirements and the wide variety of components on the market today, it is worth a look at the unique hazards in a medical setting and the evolution of connector functionality.
Safety compliance
In the ethic of first do no harm, the first priority for FDA approval ensures that electrical devices do not add problems to the clinical environment. Patients and medical workers should be protected from the current flowing between devices.
The #1 and #2 rankings of first numeral of Ingress Prevention (IP) rating -- see table – reflects the need for suitable dielectric material around cabling and connection points.
Ingress Protection (IP) Rating Chart – First Number |
|
Protection against solid objects |
|
0 |
No protection |
1 |
Protected against solid objects over 50mm (e.g. accidental touch by hands) |
2 |
Protected against solid objects over 12 mm (e.g. fingers) |
3 |
Protected against solid objects over 2.5 mm (e.g. tools, wires) |
4 |
Protected against solid objects over 1mm (e.g. tools, wires) |
5 |
Protected against dust – limited ingress (no harmful deposit) |
6 |
Totally protected against dust |
Both the numbers together form the complete IP rating of a connector or component:
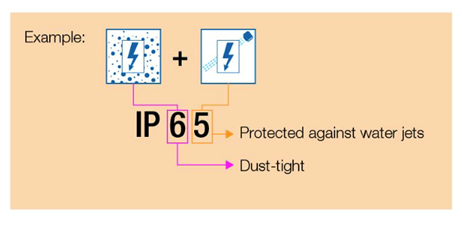
The FDA also seeks safety for other electronic equipment. Devices and connectors should have adequate shielding to prevent electromagnetic interference (EMI).
Simple enough so far. But safety issues in healthcare go a lot further.
Medical Connector Reliability
Once electric devices are in operation for patient care, the next hazard is the unintended removal or failure of power. A piece of equipment could cause a short circuit or residual current, for example, and trigger protective mechanisms in the network, which might shut down possibly life-sustaining equipment elsewhere.
In the past, misconnections were a major source of power or data signal failure. With consumer electronics, it is not uncommon to trip on a cord, yank a connector out of its socket, or spend a few seconds figuring out which cable goes where. In a hospital setting, however, these small interruptions can have serious consequences.
More robust methods have been developed to ensure reliable coupling for medical connectors that are attached and detached in the rush of emergency. These modifications include push-pull, quick disconnect, breakaway, bayonet, and blind- and screw-mating. Blind mating is for situations where the connection point lacks a clear line of sight. Push-pull designs have an audible click to indicate secure engagement.
Medical applications that need frequent attachment typically demand more rugged connection components which can stand up to 10,000 mating cycles. Some cabling systems include overmolding between the cable insulation and plug material to provide extra durability.
Even minor ease-of-use considerations - a system of color-coded plugs and receptacles or mechanically unique interconnects - can save medical personnel valuable time and prevent critical errors.
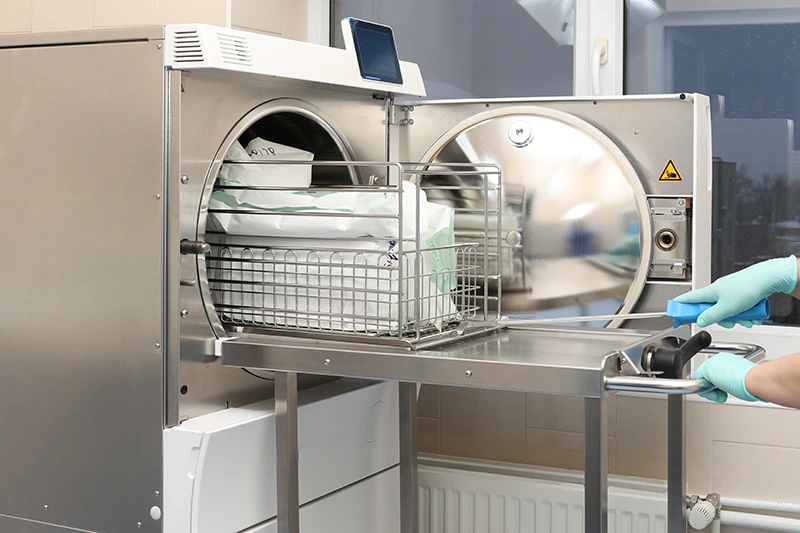
Connector Sterilization
Some of the most handled objects in a hospital setting are cable endpoints. These constitute a different kind of safety concern: cross contamination.
Clinical workplaces mitigate risk of infection by the routine cleaning of equipment. Housing and cabling of electronics need to be resilient when exposed to the common methods of sterilization:
- Gamma irradiation – the radiation method avoids the use moisture and high temperatures, yet has a drawback in that high doses of gamma rays can degrade semiconductors and polymers.
- Autoclave – an old sterilization process involving steam and pressure, which would require temperature- and moisture-resistant components.
- Chemical treatments - Hydrogen Peroxide Plasma Sterilization - such as STERRAD® - uses H2O2 and low-temperature gas plasma to rapidly sterilize medical devices without leaving toxic residue. Another process, Ethylene Oxide (EtO) gas sterilization, cleans materials without extremes in temperature or exposure to liquids.
PPSU, PSU and PEI, three common thermoplastic plastics frequently used in the medical field, feature different combinations of thermal, electric, and mechanical properties and can offer resistance to the techniques above. Additionally, soak caps to cover receptacles often accompany devices and protect contacts during sterilization.
Knowledge of the expected method of cleaning on site can help engineers select connectors with the right temperature, radiation, and chemical protection.
Dirt and Moisture
Keeping patients away from microbes is one point of cleaning. Electronics themselves, like ICs, are also susceptible to evasive fungi, bacteria, viruses, and spores. And it goes without saying that water causes circuits to short.
Where the first-numeral in the IP Rating 1-3 protects larger objects: users, equipment, and wires from current through the device, the numerals ranked 4-6 in the table above pertain to the device’s resistance to smaller objects: dirt and dust.
The second numeral of the IP rating, listed in the table below, ranks the degree of moisture resistance.
IP Rating Chart – Second Number |
|
Protection against liquids |
|
0 |
No protection |
1 |
Protected against vertically falling drops of water |
2 |
Protected against direct sprays up to 15” from the vertical |
3 |
Protected against direct sprays up to 60” from the vertical |
4 |
Protected against sprays from all directions – limited ingress permitted |
5 |
Protected against low pressure jets from all directions – limited ingress permitted |
6 |
Protected against strong jets of water – limited ingress permitted |
7 |
Protected against the effects of temporary immersion between 15cm and 1m for 30 min |
8 |
Protected against long periods of immersion under pressure |
Medical interconnects should have a matching rating between cable and mating receptacle. For example, an IP67 system is near maximal, with protection against the finest dust particles (6) as well as immersion under 1 meter of water for up to a half hour (7).
Whether for diagnostic imaging, patient monitoring, portable devices, or assistance in surgery, medical devices and their connectors need effective seals for IP.
Making the right connection
Many times, compliance, ease-of-use, and IP concerns can run counter to other design factors, such as weight, cost, and size. Choosing which terminals, cables, and connector styles requires some forethought and research into end use in the clinical setting.
Experts at large electronics suppliers such as NorComp can be a valuable resource in finding the right combination of attributes for your medical project and, if needed, can produce customized connectors.
Explore some of the most commonly used medical components in stock at NorComp, which include features like high IP ratings, push-pull locking mechanisms, EMI protection, and chemical-wash resistance.
Go Back