Products
- Circular Connectors & Cable Assemblies
- D-Sub Connectors
- IP67 D-Sub Connectors
- D-Sub Backshells
- Micro-D Connectors & Cable Assemblies
- Power-D & Combo Mixed Connectors
- Push Pull Connectors
- D-Sub & Micro D Hardware
- Modular RJ45 Connectors
- USB Connectors
- D-Sub Adapters & Gender Changers
- SCSI .085"/.050"
- .050 Ribbon
- Headers & Receptacles
- Bayonet Connectors
Designing Connectors for Rugged Environments
Today’s electronic systems require connectors to supply both power and data between subsystems, but not all connectors are created equal. Connectors intended for deployment in harsh environments need to be carefully evaluated to ensure they perform as expected in the end application.
In addition to environmental considerations, these connectors must offer a balance between power handling and signal integrity in advanced applications like robotics and embedded computing. Yet another aspect of selecting rugged connectors is form factor; some rugged connectors may be too bulky for the system being designed, but smaller form factors may be too delicate for the intended application.
How can designers best balance these aspects of connector design and selection? When procuring connectors and cable assemblies, be they standard or custom - which performance requirements should take precedence?
Designers and engineers who require ruggedized connectors should pay close attention to all relevant supplier specifications. If you’re design requires a custom connector or cable assembly, you need to identify and communicate the critical specifications and performance requirements to your manufacturer early in the design process.
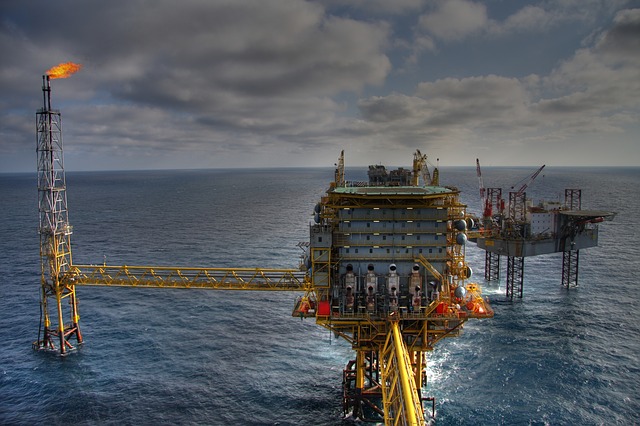
Rugged Connector Specifications for Use in Harsh Environments
Different product designers and engineers will have different definitions of what exactly constitutes a “rugged connector” or “harsh environment.” There is no one-size-fits-all solution, but there are some specifications that stand out as prominent for various applications. Common operating conditions for rugged connectors can include:
- Extreme temperatures
- Exposure to contaminants like water and dust
- Exposure to corrosive liquids or gasses
- Exposure to radiation
- Emission and reception of electronic noise
- High or low pressure environments
- Deployment in areas with high vibration
Ingress and Corrosion Protection
The first place to start when selecting rugged connectors is to consider where the end unit will be deployed, namely environmental conditions and exposure to corrosive substances.
Ruggedized connectors that are to be used in outdoor environments must be sealed against moisture, dust, and other external contaminants. These connectors should be designed to meet industry standard IP67/IP68 requirements.
Connector materials and finishes are also an important point of consideration as exposed surfaces could corrode over time. In shielded systems, such as in certain industrial settings,
connectors with a stainless steel or aluminum shell are usually the best choice.
Alternatively, connectors using advanced plastic compounds may be very useful in non-shielded applications where extreme corrosion is a risk.
Contact Size and Power Handling
Contact specifications are important for products that require high reliability in industrial-grade, power applications. Both contact size and wire gauge will determine the connectors amperage capacity (typically 10 to 40 amps), and larger contact sizes will be required when a system’s power requirements exceed 5 amps in any given circuit.
Designers need to balance the space requirements of a physically larger connector (with its added weight and mounting requirements) with the actual power requirements of the system.
Retention and Keying
In harsh mechanical environments, connectors or cables may experience jerks or pulls that cause them to be disconnected or damaged. Most ruggedized connector systems include robust mechanical locking systems to prevent against disconnect or damage. Alternatively, there are retention mechanisms included in some connector housings that allow a connection to be broken once a certain amount of force is applied.
In addition to mechanical retention, connectors are available with a wide range of keying features to ensure proper mating orientation and to prevent crossed connections in multiple connector & cable bundle applications.
Shielding
Some systems have very high EMI/EMC requirements on conducted noise or ESD, which are enforced in industry standards. This is certainly a concern for rugged connectors that need to carry high speed digital data.
Shielded connectors are an option that can help block external noise, but they may not be enough to pass EMC testing for demanding applications (e.g., MIL-STD-461 compliant products). Shielded connectors will often be used with a braided cable that provides additional radiation reception/emission suppression. These connectors can also provide the same sealing and corrosion resistance benefits as other cables that may not be electrically shielded.
Cycling
Finally, there is cycling to consider. All connectors have a finite number of mating cycles they can withstand before the electrical contacts in the connector start to wear out. Once this limit is reached, the contacts on the connector will visibly wear and the contact resistance will increase.
Standard connectors typically range from 100 to 500 mating cycles , but significantly higher cycle duties (5,000+) can be achieved for rugged applications through advanced contact design and higher plating thicknesses.
Custom Connector and Cable Assemblies
The above specifications apply to off-the-shelf connectors with standard form factor and pinouts, as well as to custom connector and cable assemblies. Manufacturers of rugged connectors can customize a solution for most commercial and industrial-grade applications, including ruggedized overmolded versions of standard connectors.
This gives design engineers one way to create custom ruggedized connector and cable assemblies that still provide data over standardized protocols and power over secure, high reliability connections. Designers that want maximum reliability should take a look at the design options above and match these to their intended deployment environment.
When you need rugged connectors for deployment in harsh environments, look to NorComp for standardized or customizable interconnect solutions. NorComp’s product lines are Rugged Environment Certified (REC) and are ideal for use in robotics, military, industrial equipment, and other demanding applications. Contact Norcomp today to learn more about our standard or custom interconnect solutions.
Go Back